The all new Travel family.
Discover your perfect companion for every journey.
Torqeedo: Leading electric boat motors & maritime propulsion systems
RECREATIONAL
COMMERCIAL
Electric stories
TORQEEDO OUTBOARDS AVAILABLE THROUGH YAMAHA DEALERS
From January 2025, selected Torqeedo outboards will be available for the first time in eight European countries through the Yamaha dealer network.
READ MORE
READ MORE
Press Release
THE DRAGON OF LAKE STARNBERG
See how an electric motor improves a day on the water: the new Travel 903 delights even experienced sailors with its increased range and efficiency. A sailing trip on Lake Starnberg near Munich – with winds at 15 knots of wind and without gasoline fumes.
READ MORE
READ MORE
Press Release
FIRST HYDROGEN-POWERED RIB HITS THE WATER
This summer, the world of competitive sailing is set to witness a historic moment as the Dutch sailing organization introduces their first-ever emission-free, hydrogen-powered coach boat, equipped with a Torqeedo Deep Blue electric motor. Learn why this is a pivotal moment in the effort to protect our climate and local air quality.
READ MORE
READ MORE

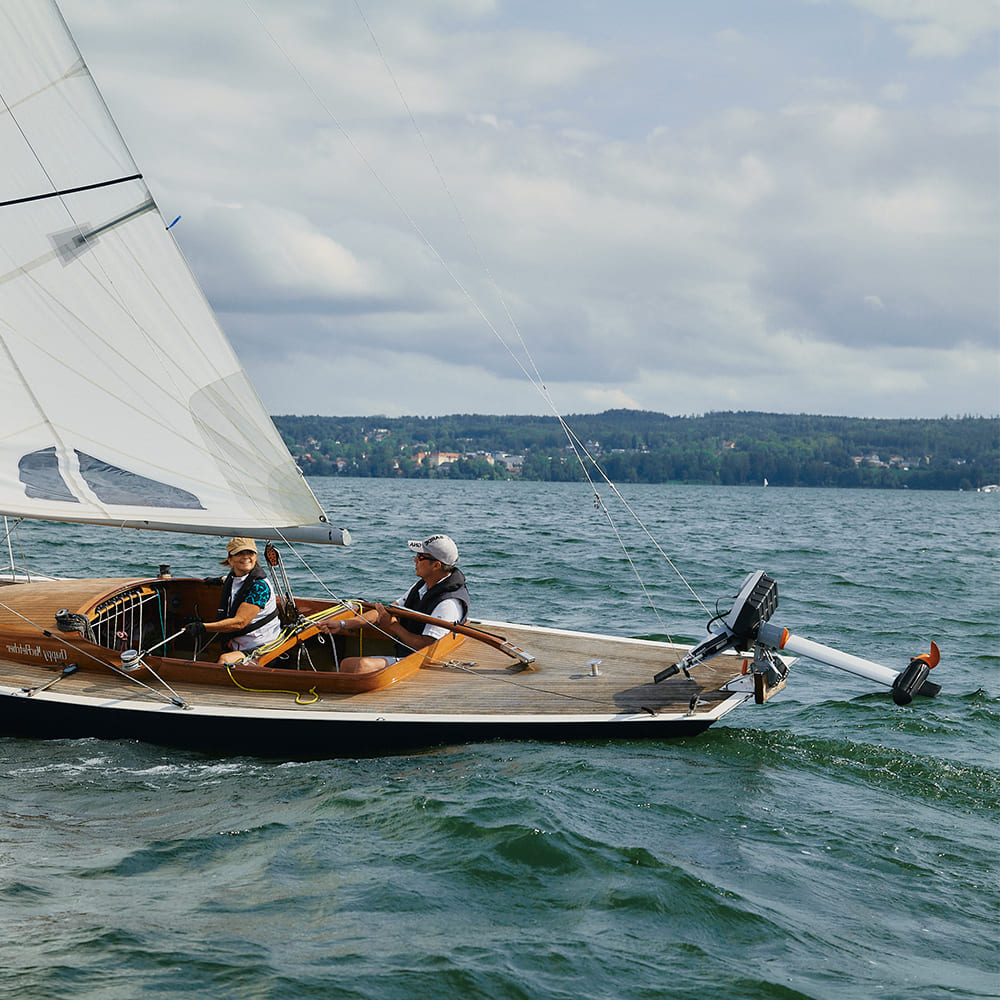
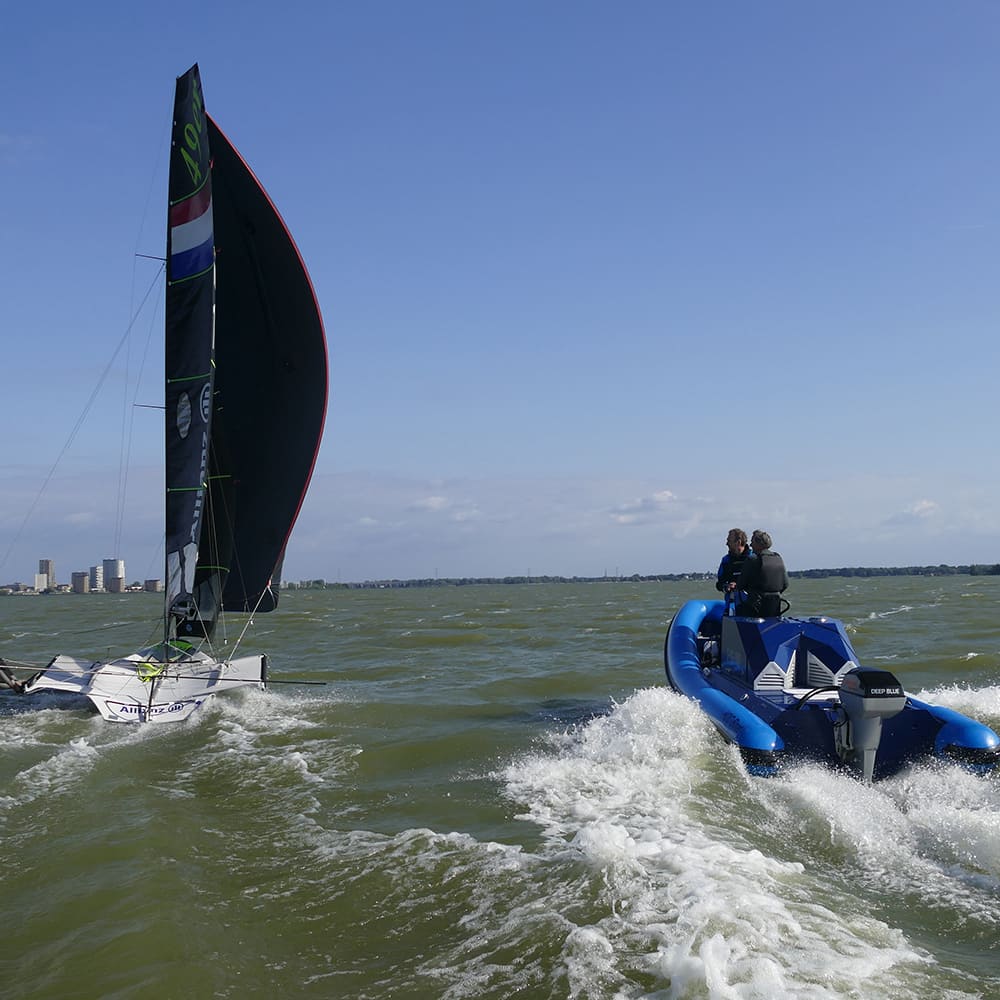